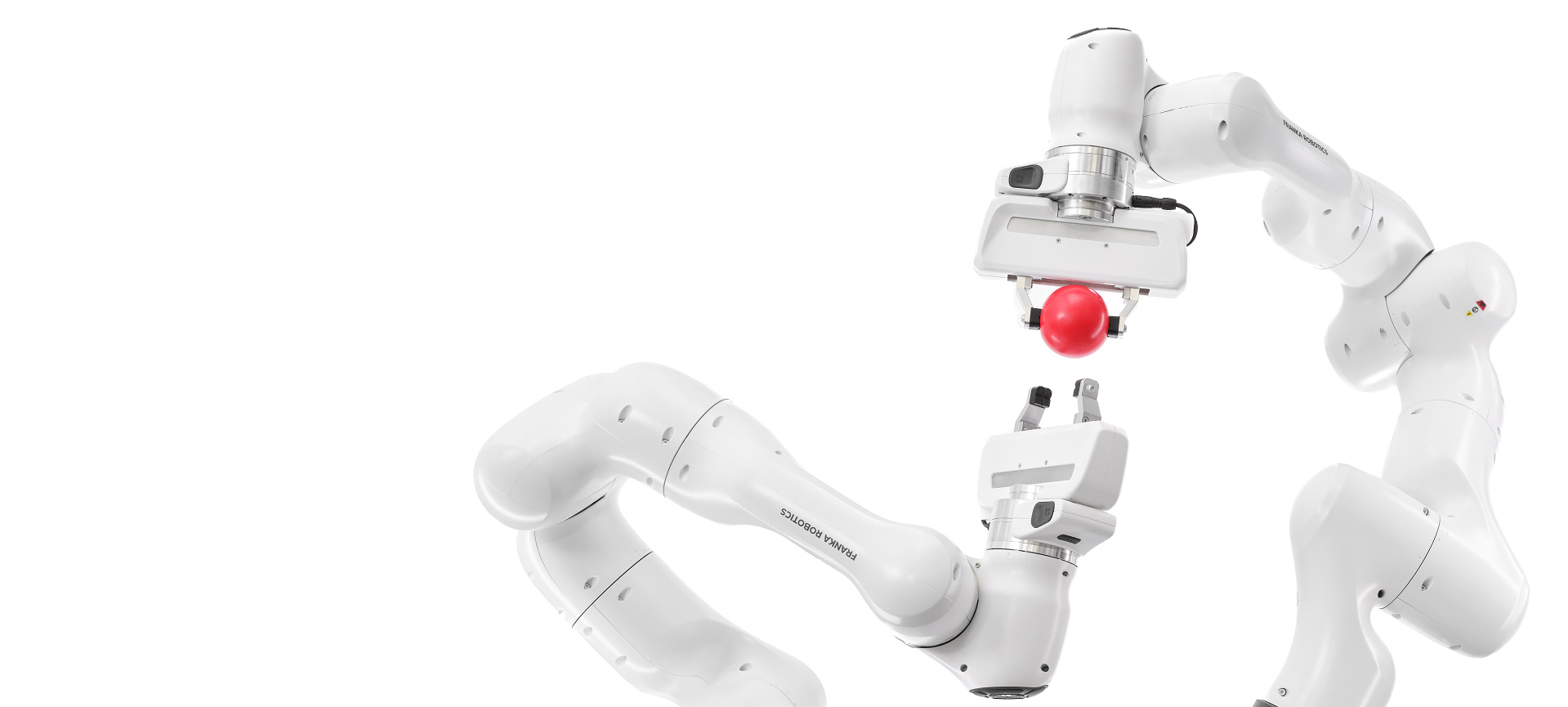
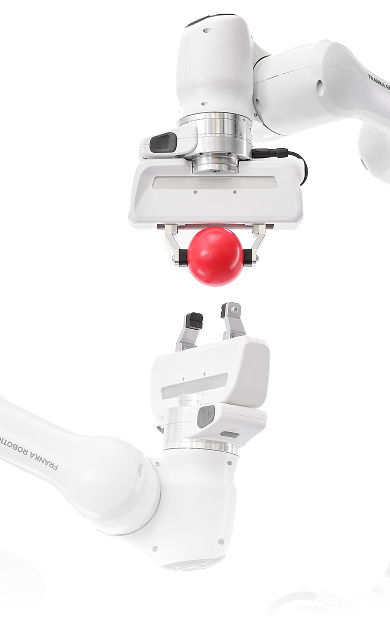
FRANKA RESEARCH 3
Franka Research 3 is the reference world-class, force-sensitive robot system tailored for AI and robotics research. It empowers researchers with easy-to-use robot features as well as with low-level access to robot’s control and learning capabilities.
Find out more about all features of FR3.
Get a free technical presentation
with our experts!
Franka Research 3 is the reference world-class, force-sensitive robot system tailored for AI and robotics research. It empowers researchers with easy-to-use robot features as well as with low-level access to robot’s control and learning capabilities.
Find out more about all features of FR3.
Get a free technical presentation
with our experts!
-
High-Quality Mechatronic System
Engineered and manufactured in Germany, Franka Research 3 is a reliable robot system, TÜV certified for human-robot collaboration. FR3 is equipped with high-quality sensors, best-in-class actuators and is optimized for performance and ergonomics.
-
Human-like Dexterity
The 7 degrees of freedom Arm of Franka Research 3 offers human-like dexterity, enabling motions in tight spaces and around obstacles.
-
High Sensitivity
The torque sensors integrated at each joint finely estimate external contact forces, and the fast control loop enables prompt reaction to collisions. The high sensitivity permits advanced torque or force control possibilities and provides smooth and intuitive hand-guiding capabilities.
-
Versatile Control Interfaces
From the most intuitive programming UI for quick task setup to advanced direct joint control for deep research, Franka Research 3 adapts to the needs of every user.
-
Advanced Motion Control
High-frequency (1 kHz) motion control with a low-level, high-quality sensor data interface, ideal for motion control research and the development of highly specific behaviors, unachievable with most robots.
-
Open and Collaborative Platform
Join our global community of top robotics researchers, and integrate seamlessly with the leading open-source frameworks such as ROS 2, MATLAB and many others to reproduce, advance and share cutting-edge research.


ISO 13849
DISCOVER THE LATEST UPGRADES
Stay ahead with our newest features, extensions, and optimizations. FR3 and its software are continuously progressing, via free over-the-air updates.
-
ENHANCED USABILITYFR3 Arm v2.0With intuitive joint rotation markings and X/Y axis indicators, plus a sleek, modern look, the new design is as functional as it is eye-catching.
-
DESK APISystem Img v5.8
The new Desk API enables you to programmatically administrate and operate FR3. Progammatically open the brakes and activate FCI, clear safety violations and much more!
-
TORQUE CALIBRATIONSystem Img v5.8Directly in the field, recalibrate the internal torque sensors to deliver consistent accuracy during the complete lifetime.
-
MUJOCO SUPPORTFrom the communityPower up your simulations with MUJOCO, offering a seamless experience for modeling and testing.
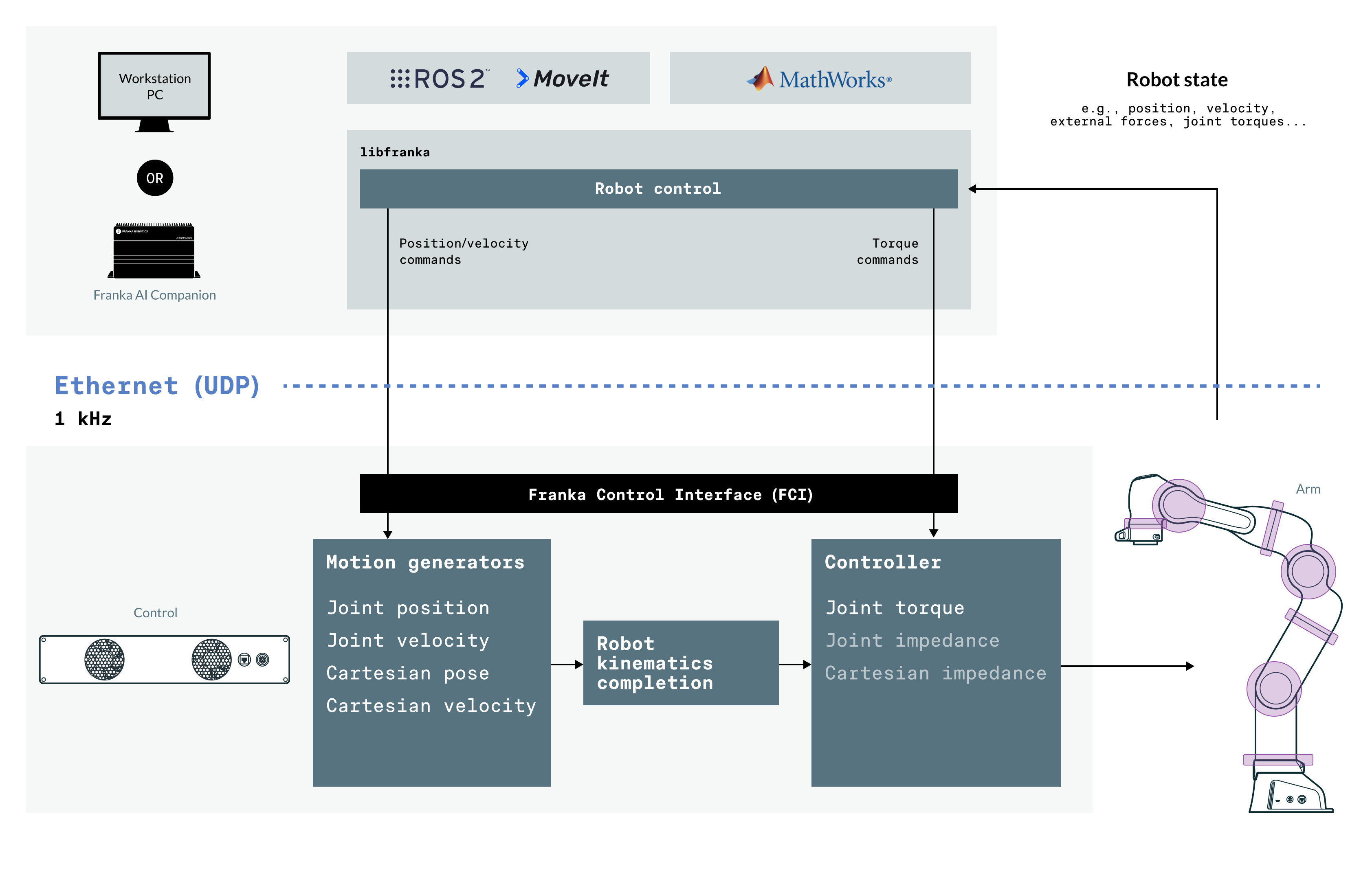
FRANKA CONTROL INTERFACE (FCI)
-
DIRECT CONTROLFCI provides low-level, real-time control of the robot, without internal transformation. Internal supervision only prevents self-damage. Gain access to the control loop, including position, velocity and torque in joint space, as well as position and velocity in Cartesian space.
-
DATA ACQUISITIONCapture system state data from sensors and models at 1 kHz. FCI also provides external force estimation and additional insights.
-
COMMUNITYJoin the ever-growing Franka Robotics community and leverage C++, ROS 2, or MATLAB & Simulink to accelerate robotics innovation.
-
SAFETYImplement custom safety rules to ensure operator protection.
-
-
REAL-TIME CONTROL AND ROS INTEGRATION
The Franka Control Interface (FCI) allows a fast and direct low-level bidirectional connection to the Arm and Hand. It provides the current status of the robot and enables its direct control with an external workstation PC connected via Ethernet. By using libfranka, our open source C++ interface, you can send real-time control values at 1 kHz with 5 different interfaces:
- Joint level torque commands with gravity and friction compensation.
- Joint position or velocity commands.
- Cartesian pose or velocity commands.
Simultaneously, you gain access to 1 kHz measurements of: - Joint data, e.g., the position, velocity and link side torque sensor signals.
- Estimation of externally applied torques and forces.
- Various collision and contact information.
The robot model library provides: - Forward kinematics of all robot joints.
- Jacobian matrix of all robot joints.
- Dynamics, inertia matrix, Coriolis and gravity vector.
Additionally, franka_ros connects Franka robots with the entire ROS 2 ecosystem, integrating libfranka into ROS 2 Control. It includes URDF models and detailed 3D meshes of our robots and end effectors, which allows visualization (e.g., RViz) and and Gazebo simulation. And the MoveIt! integration simplifies motion planning and gripper control, with example implementations demonstrating how to operate the robot using ROS 2.
THE RIGHT INTERFACE FOR EACH USE CASE
Three access levels to the robot address different needs and skills,
for the whole spectrum of robotics research.
-
DESK
The ease of use and minimal programming time makes Desk the most suitable interface for rapid prototyping, simple human robot interaction studies and demos.
-
RIDE
It enables researchers to fully integrate the Franka Robotics system into experimental setups, and exploit its integrated high performance controllers. It is also a great tool for teaching introductory robotics.
-
FCI
FCI bypasses the robot’s Control to let researchers run their own control algorithms in external real-time capable PCs at 1 kHz. It is the ideal interface to explore low-level planning and control schemes.
DESK | RIDE | FCI | |
Workflow-based programming using Apps | |||
Quick prototyping of experiments and demos | |||
Execution of robot tasks | |||
Development of customized Apps | |||
Connection of third-party hardware | |||
Connection of external resources | |||
1 kHz torque, position and velocity control | |||
1 kHz measurement of sensor signals and robot status | |||
Access to kinematic and dynamic robot model | |||
Integration with ROS and MATLAB & Simulink |
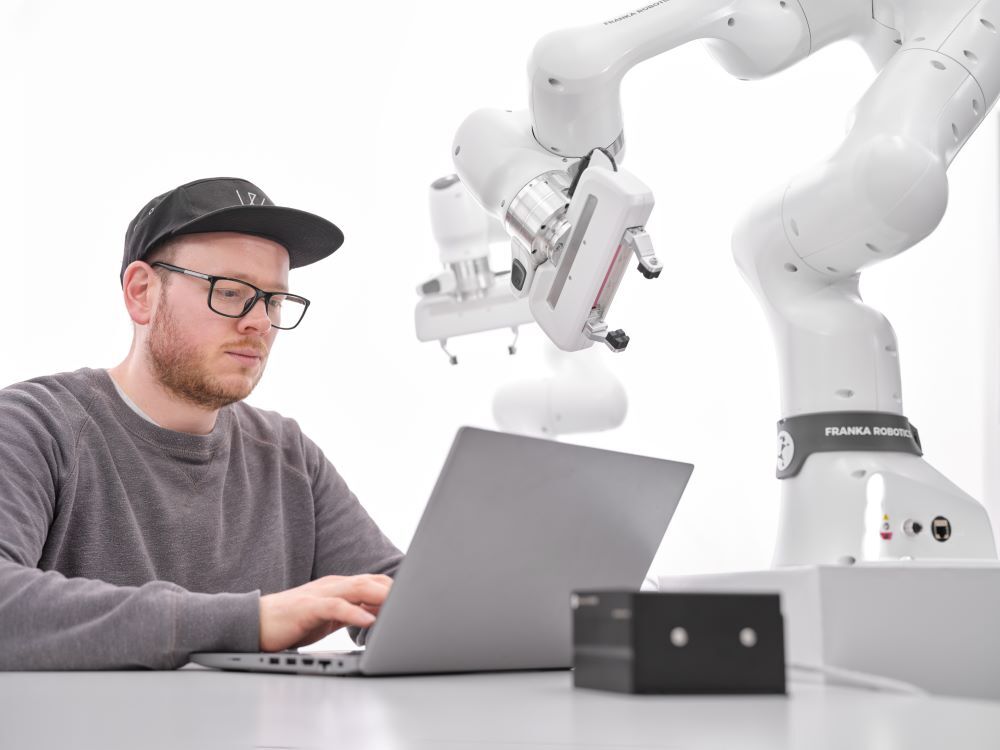
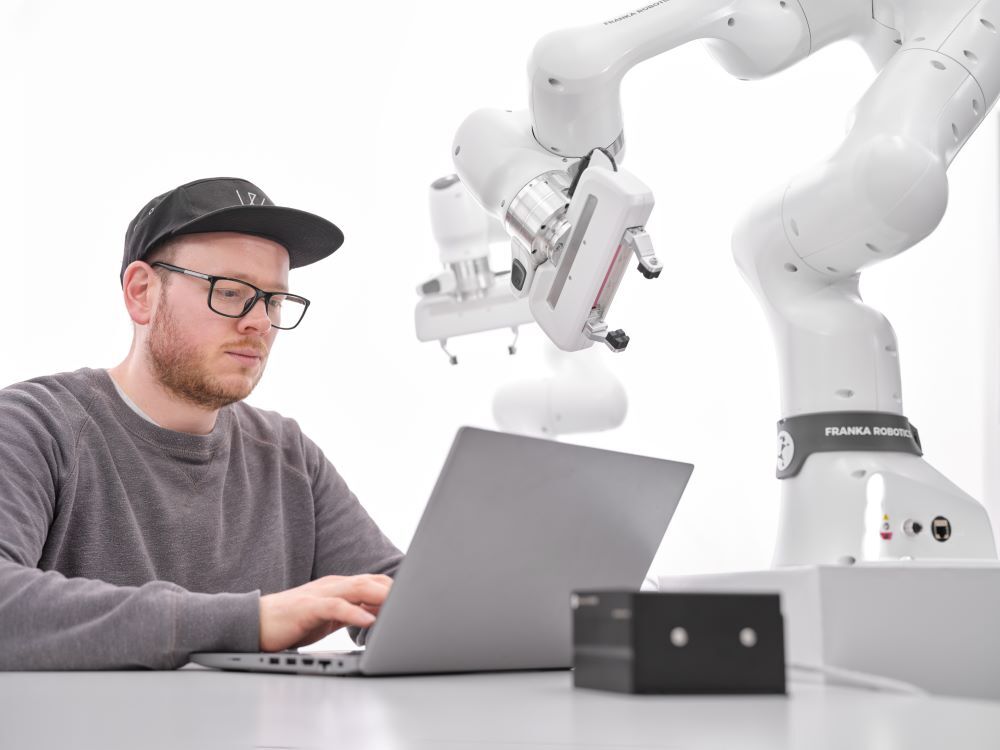
DISCOVER HOW TO ENHANCE YOUR ROBOT SYSTEM
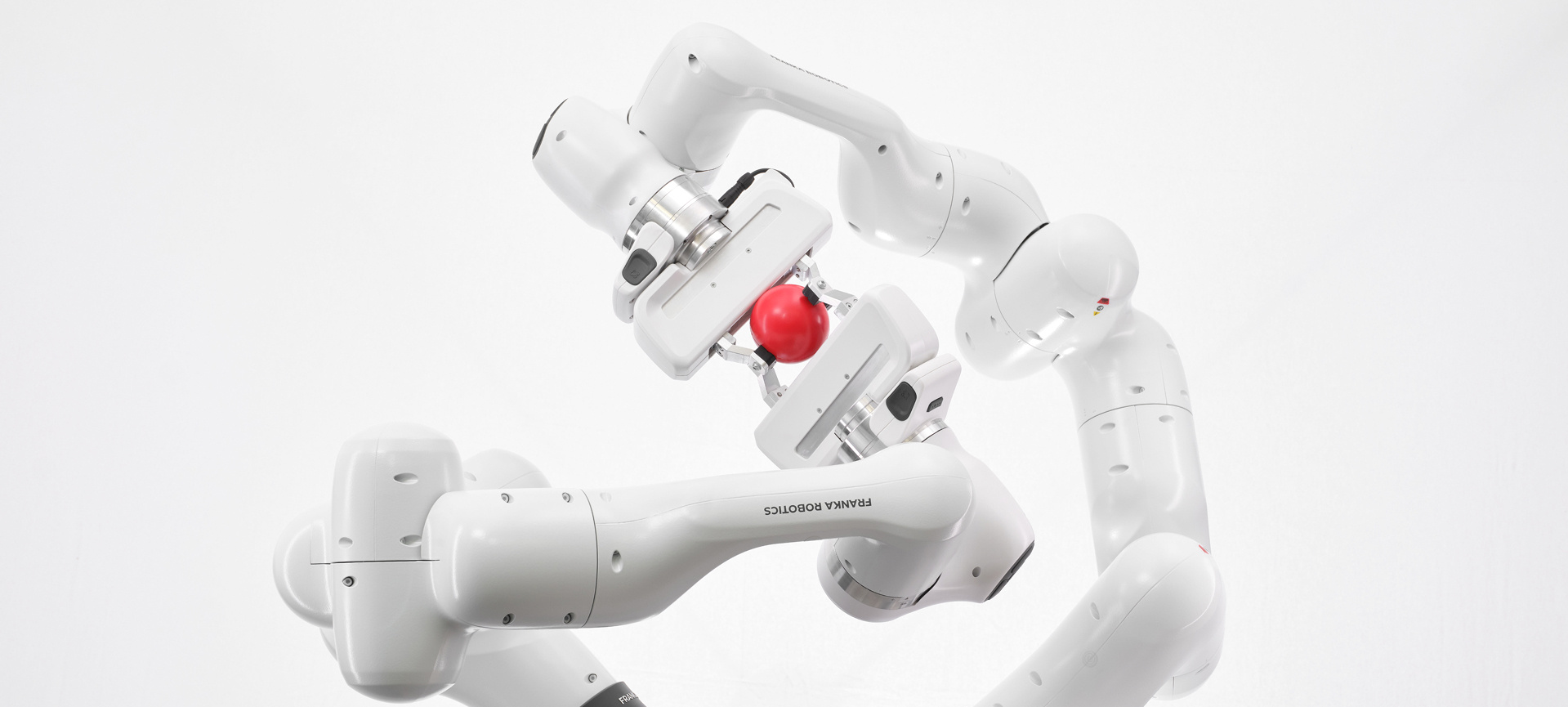
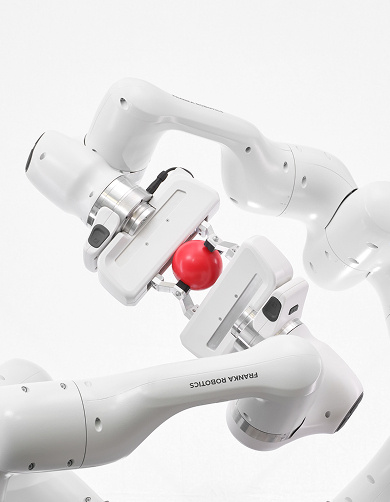
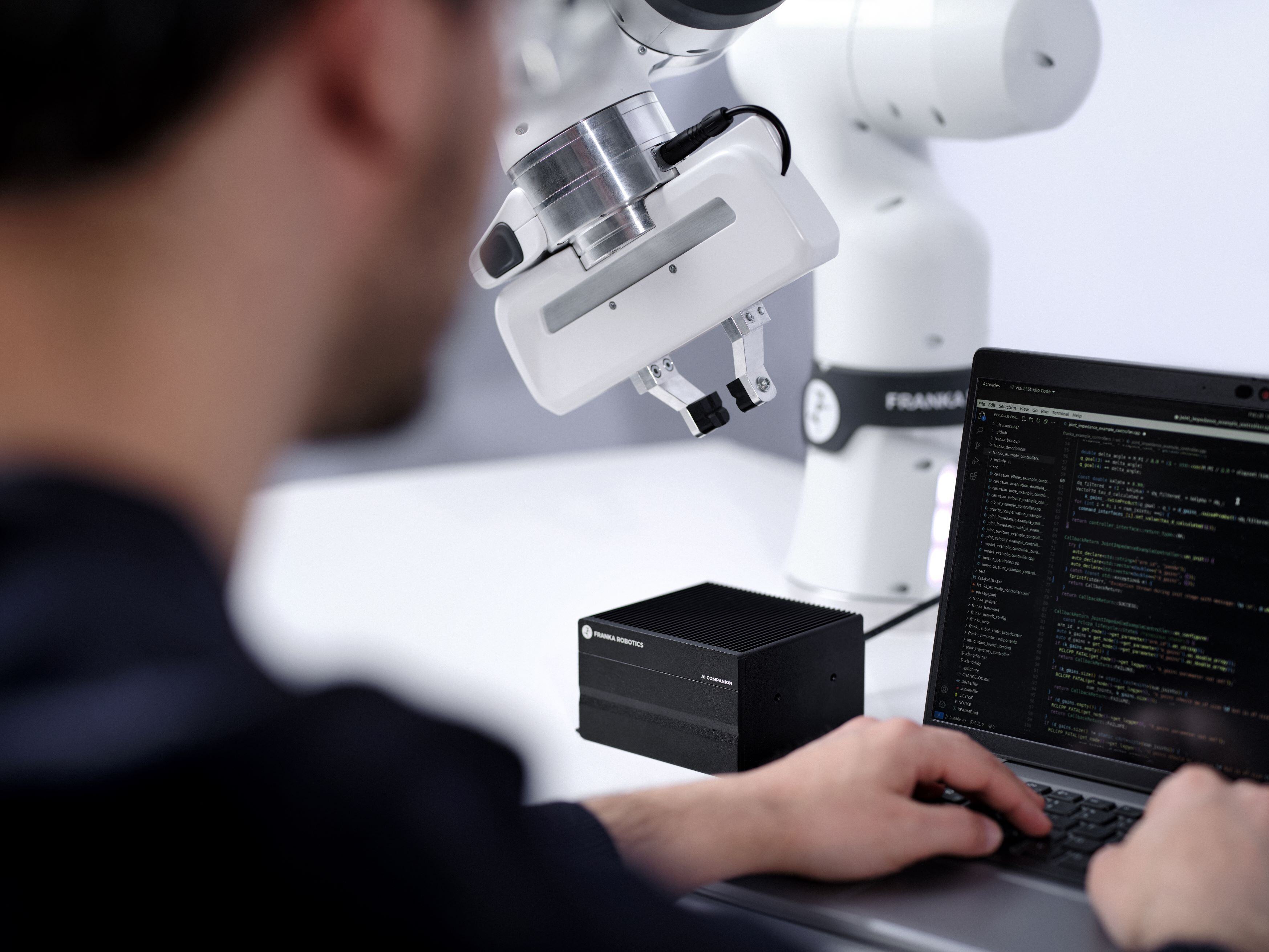
DEVELOP ON THE FRANKA ROBOT PLATFORM
The resource hub for developers working with the Franka Research 3 robot platform. Dive into a wealth of tools, libraries and documentation designed to accelerate your development journey. Whether you're a seasoned developer or just starting out, you'll find everything you need to build, create and innovate.
REQUEST A QUOTE
We'd love to hear from you! Please fill out the form and we'll get back to you as soon as possible.
The process is quick and easy:
1. Fill out the form with your details and requirements.
2. A member of our team might reach out to discuss your goals in more detail.
3. We'll provide a tailored solution and a quote that fit your needs.
Let’s start the conversation today!